Offering a unique user's perspective from his 363 days in orbit, Alexander described out-of-Earth manufacturing as a game-changer for space exploration.
"It's mind boggling to think of what the ISS actually is," Alexander began. "We built it in space, moving at 28,000 km/h, out of modules manufactured in different continents and put together in orbit for the first time. Those of you who have built a house, could you imagine doing it without being able to go to Home Depot in case you forgot some screws or something?"
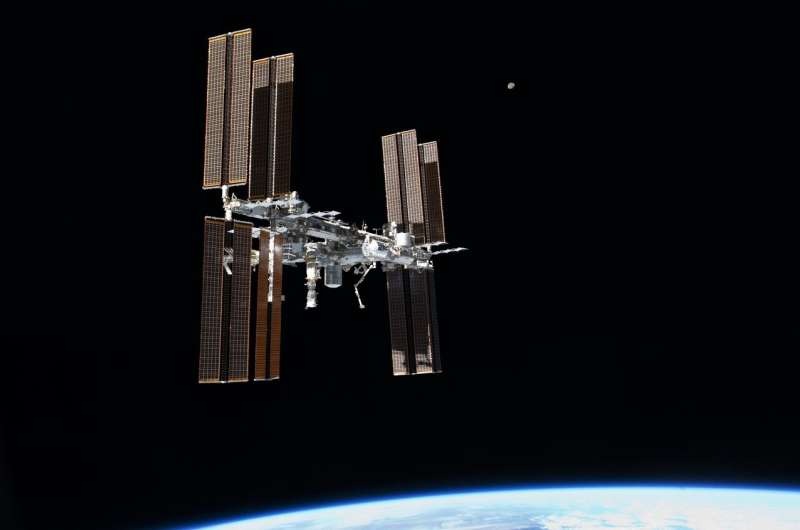
Figuring out a fix
He described the ISS as a symbiosis of humans and robotic systems, with human bringing the skills that robots do not have—especially when something goes wrong.
"For instance, we worked on more than 600 different scientific experiments during my Blue Dot and Horizons missions to the ISS, but one I'm particularly fond of is the Electromagnetic Levitator, a microgravity furnace for metals. It feels a little bit like my baby: it was a lot of work to install in the European Columbus Laboratory, because a bolt securing it in place for the launch got stuck during the installation, and threatened the entire experiment.
"After a lot of analysis we decided to saw off the bolt, and I suggested to cover the saw blade with my shaving gel—to catch any metal shavings which otherwise would have been floating around dangerously.
"Then there was the time a clamp got sucked deep inside a ventilation duct, and I had to spend a couple of hours fishing it out with a hook I'd stuck on a flexible pole."
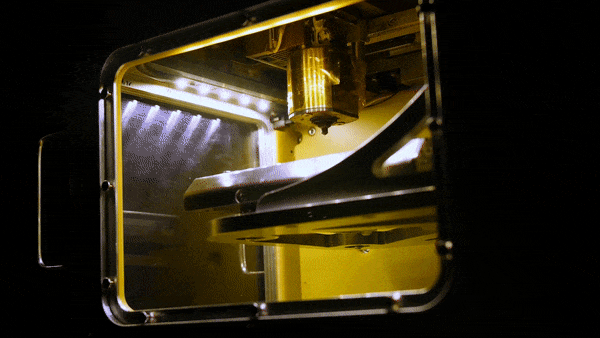
Another example of improvisation was more personal: "I made a candle actually, out of shiny Kapton tape and an old flashlight, for my crewmate's birthday. I didn't tell the ground about it but we ended up putting it up all the time for dinner—as a sign the workday was over and it was time for a mental break. Eventually we got a call from the safety guys who must have seen it on a photo and said 'don't be offended, but is it possible you have a candle up there?" It was a great and humorous compliment—they thought it might be a real candle!
"That shows how important the small things are in space: with out-of-Earth manufacturing you might even imagine, on the way to Mars, a crewmember's daughter making a kindergarten sculpture for their birthday, then the crew member prints it on board and puts it up in their crew quarters."
Aboard the ISS, missing items can eventually be sent up on the next supply rocket—which will not be the case for interplanetary expeditions. Alexander stated that out-of-Earth manufacturing will become really important during long-duration missions away from our home world.
Alexander provided a list of potential use-cases, including large bulky items, mechanical mounts and adapters, coverings and specialized tools, and eventually food and even biological material for medical purposes. The ability to recycle all these parts for subsequent reprintings also would be a big plus.
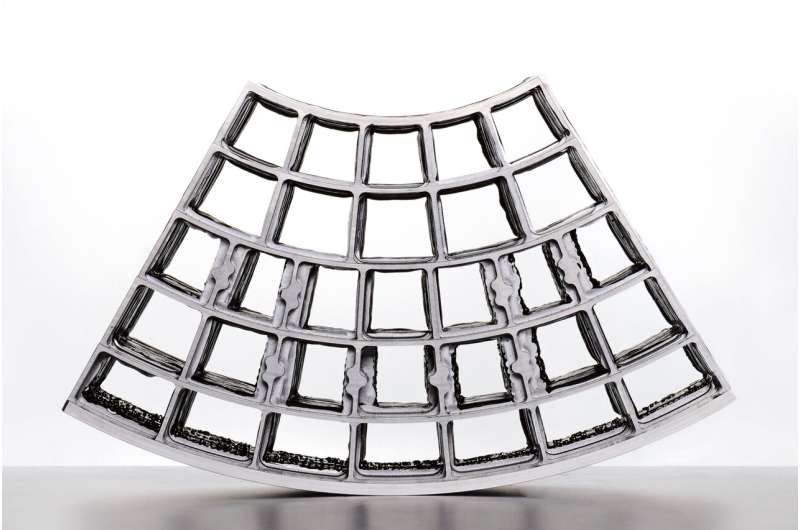
3D printing, from ground to space
Typically the actual design work for out-of-Earth manufacturing would be done on the ground—but it is important that those on the ground have an accurate picture of conditions in space. "Most ground teams have the impression the in-orbit configuration is known very precisely, but often this isn't the case: records might be outdated, and configurations change over time."
Alexander gave the example of his Russian colleagues trying to apply plastic coverings to renew the internal wall surfaces of the service module, but finding that some of the shapes that had been produced did not match the reality after two decades in orbit, and had to be modified to fit.
"The real key enabler is actually a closed feedback loop, with a measuring and scanning system to get precise data on geometries and configurations before designing the tool for printing, and also as a quality control method afterwards."
Only on highly autonomous missions, such as trips to Mars, would the crew undertake the entire production cycle themselves, without ground assistance—or else during emergencies.
Alexander concluded: "To leave Earth the most important governing law is the rocket equation, but to live in space the most important is Murphy's Law—you have to have the mindset that whatever can go wrong might eventually go wrong. We'd better be prepared for that, and in-space manufacturing will help us with that. It's an enabling game-changer to let us go further into space and reduce the risk. So I welcome the out-of-Earth manufacturing effort from ESA to help Europe secure a leadership position in this promising domain."
ESA's Advanced Manufacturing initiative
"This workshop took place as part of ESA's Advanced Manufacturing initiative, to show the state of the art in manufacturing technologies and reach out to the community as an opportunity to discuss a future vision and strategy," notes Thomas Rohr, heading ESA's Materials and Processes Section.
"Our more than 40 technology development activities kicked-off so far open up new possibilities in terms of design freedom, streamlined production stages and reduced cost or lead time, along with enhanced product performance—and extending the manufacturing process to space out of Earth is a crucial element of our overall efforts with great potential for future mission scenarios and commercial business cases."